The principle of laser cutting
What is laser cutting?
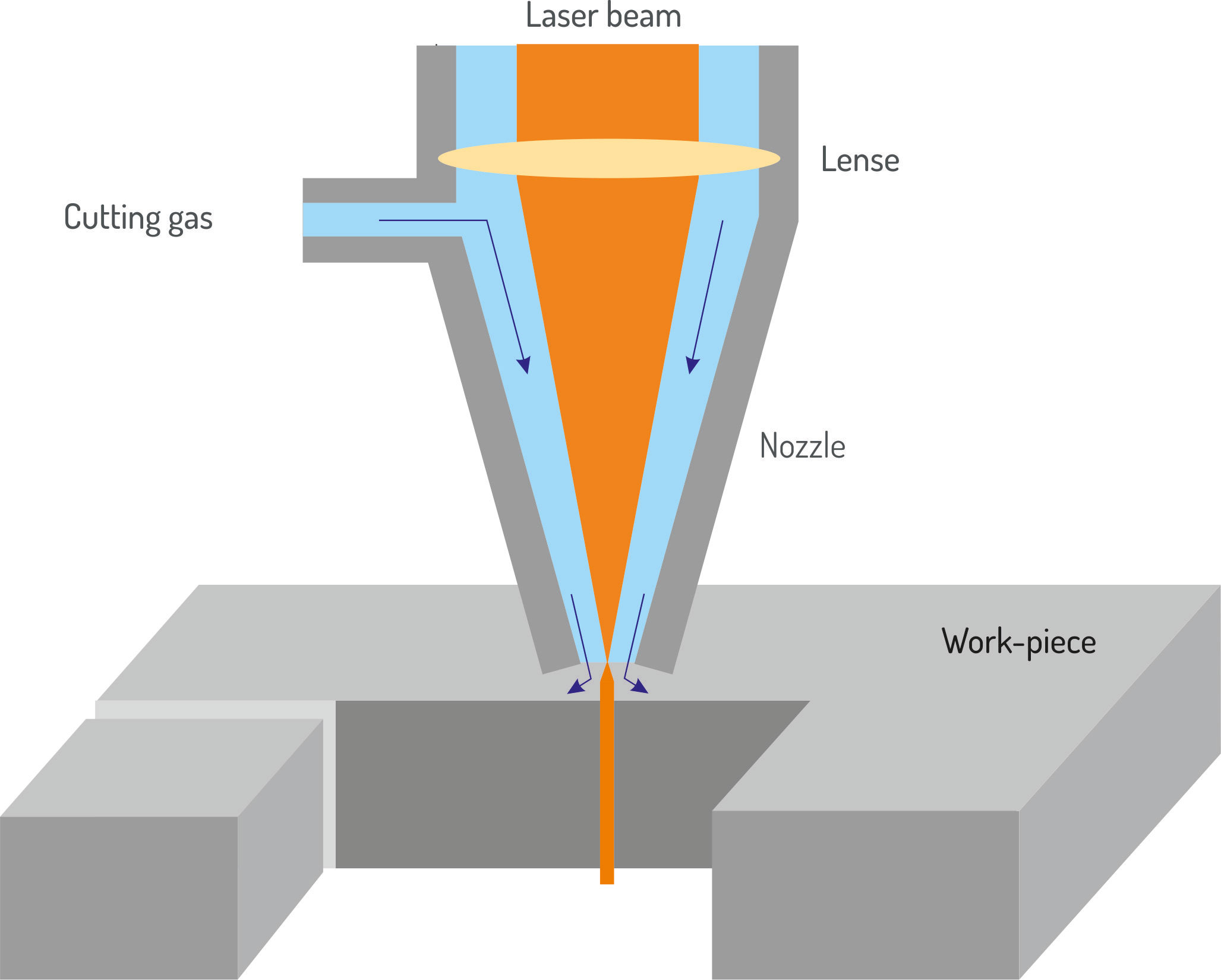
Laser cutting is a thermal separation process for cutting electrically conductive as well as non-conductive materials. Due to high power density because of the strongly focussed laser beam on the workpiece surface, the material melts in the kerf or vaporises. A coaxial gas beam gives crucial support to this process because it drives the molten material or slag, the oxidised or sublimed material out of the kerf.
The term Laser is formed by the initial letters of the words "light amplification by stimulated emission of radiation". This special process of light amplification takes place in a resonator which consists of a laser-optical medium (e. g. doped glass or gas mixture), a pump source (e. g. flash lamps, diodes or high frequency) and a cooling system. Fibre lasers are a special form of solid-state lasers with a glass fibre doted with rare earth as laser-active medium.
Laser cutting is divided into laser fusion cutting (the material to be cut is melted), oxy-fuel flame cutting (exothermic reaction with the material to be cut by using oxygen as cutting gas) and laser sublimation cutting (the material to be cut is evaporated from solid to gaseous state). is Laser cutting is the preferred process for very small holes, narrow root faces, acute-angled geometries and complex component contours. One of the advantages of laser cutting is the extremely small heat input of the laser beam, a high cut quality (rectangular cut edges ans very small kerfs), high workpiece precision, the contactless processing but also the low exposure to gases, aerosols and noise.