Plasma vs. Faserlaser – Was ist der Unterschied?
Zwischen dem Plasma- und Laserschneiden besteht ein starker Wettbewerb, vor allem weil sich der Faserlaser innerhalb weniger Jahre technologisch und kostenmäßig weiterentwickelt hat. Damit stellen sich auch klassische Plasma-Endanwender die Frage, ob sie alternativ den Faserlaser für ihre Aufgaben verwenden können. Jedes Verfahren hat seine Berechtigung und je nach Einsatzbereich technologische Vorteile.
Einsatzbereich
In der metallbe- und -verarbeitenden Industrie wird eine große Bandbreite an unterschiedlichsten Materialien und Blechdicken geschnitten. Mit Plasma lassen sich metallische Werkstoffe wie Baustahl, Edelstahl, Aluminium, Kupfer, Messing, Gusseisen, folierte oder verzinkte Bleche u. v. m. schneiden. Im Gegensatz zum Faserlaser ist das Plasmaschneiden sehr flexibel in Bezug auf Materialqualität und Zustand des Bleches. Es wird keine spezielle Blechsorte oder Materialvorbehandlung benötigt und die Werkstücke können ölig, fettig, rostig sein. Mit der Technologie HotWire können sogar nichtleitende Materialien getrennt werden.
Dem Faserlaser hingegen sind Grenzen gesetzt, da zum Teil hohe Anforderungen an das zu schneidende Material bestehen. Faktoren wie Rost, Farbe, Etikett, Höhenänderungen, Rollfehler oder Rillen auf der Oberflache wirken sich negativ auf den Schnitt aus. Die Ober- und Unterseite des zu schneidenden Materials müssen sauber sein, weil die Schnittqualität erheblich von der Blechqualität abhängt. Das Schneiden stark reflektierender Materialien (Aluminium, Messing, Kupfer) ist ebenfalls kritisch.
Das Hauptanwendungsgebiet des Lasers liegt üblicherweise in einem Materialdickenbereich von 0,5 bis 15 mm. Plasmaschneidsysteme dagegen sind aufgrund des leistungsstarken Lichtbogens und der breiteren Schnittfuge eher weniger für feine Dünnblechzuschnitte geeignet und daher für Materialdicken ab 5 bis zu 160 mm ausgelegt.

Schneidgeschwindigkeit
Mit steigender Blechdicke nimmt die Schneidgeschwindigkeit des Lasers überproportional ab. Ab 10 bis 15 mm Materialdicke überwiegen die Vorteile der Plasmatechnik bezüglich Wirtschaftlichkeit und Schneidgeschwindigkeiten.
Im unteren Blechdickenbereich kann der Faserlaser bei guter Qualität sehr hohe Schneidgeschwindigkeiten realisieren – benötigt aber dementsprechend sehr hochwertige und teure Antriebs- und Steuerungstechnik, um eine hohe Dynamik zu erreichen.

Qualität
Der Laser eignet sich vor allem dort, wo dünnes Metall mit höchster Präzision und größtmöglicher Bearbeitungsgeschwindigkeit geschnitten werden muss. Filigrane Konturen und kleine Geometrien zählen zu seinen Stärken.
Mit Plasma ist eine ähnliche und ab dem mittleren Blechdickenbereich sogar bessere Qualität möglich, sofern die Bauteile nicht zu fein und komplex sind. Hier ist die Oberflächengüte eines Plasmaschnittes vom Faserlaser unerreicht. Plasma bietet selbst bei Materialstärken über 50 mm glatte und bartfreie Schnittflächen, hohe Schneidgeschwindigkeiten und nahezu nachbearbeitungsfreie Schnittergebnisse. Feine Konturen, schmale Stege und kleine Löcher sind auch mit Plasma möglich.

Die Qualität der Schnittflächen des Lasers nimmt mit steigender Materialdicke ab und die Oberflächenrauheit zu. Das wiederum begünstigt eine hartnäckige Oxidschicht auf der Schnittfläche. Für nachgelagerte Prozesse wie Schweißen oder Korrosionsschutz (Lackieren, Feuerverzinken) ist Nacharbeit erforderlich. Aufgrund der sehr dünnen Schnittfuge besteht zudem die Gefahr einer Schnittfugen-Verfüllung oder eines Verklemmens bzw. Verkantens der Bauteile.
Hinsichtlich der Rechtwinkligkeit der Schnittfläche bietet der Laser prozessbedingt Vorteile. Doch auch mit modernen Plasmaschneidanlagen sind Winkelabweichungen von ca. 2° problemlos erreichbar und für viele Nutzer völlig akzeptabel. Je nach Komplexität und Feinheit der Bauteile kann es beim Plasmaschneiden durch den nachlaufenden Lichtbogen zu leichten Verrundungen von Konturen kommen. Löcher sind ab einer Blechdicke von 5 mm und einem Verhältnis von 0,75 zur Blechdicke in guter Qualität umsetzbar.
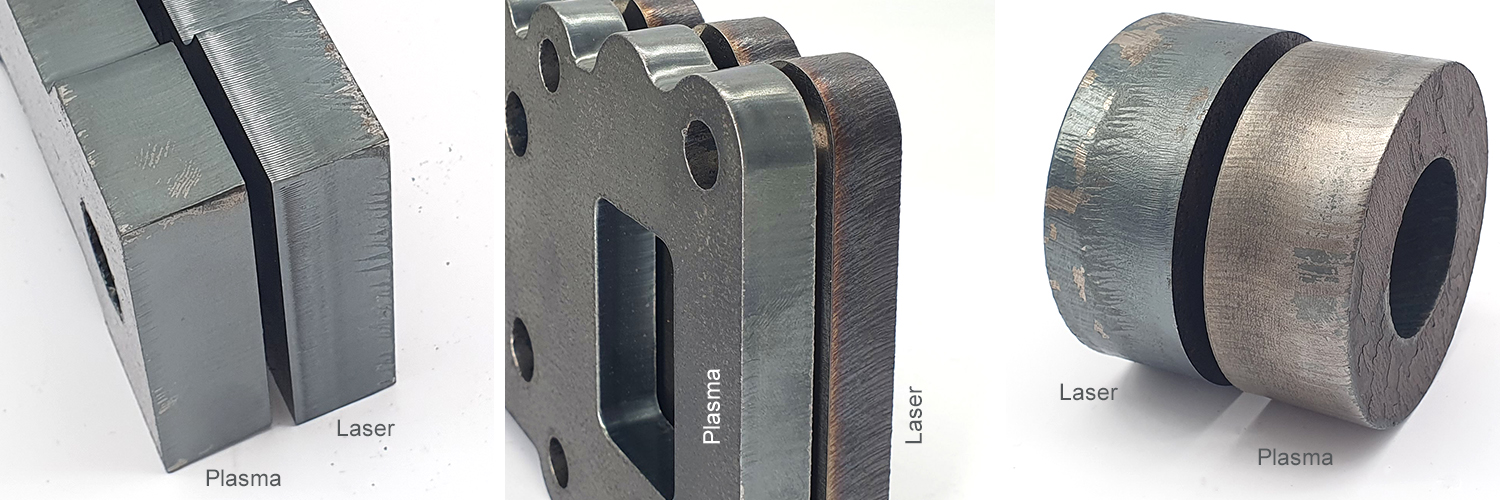
Sicherheit & Handling
Die schnelle und präzise Plasmatechnologie hat nur geringe Anforderungen an die Sicherheit und ist einfach zu erlernen und zu bedienen. In den meisten Regionen der Welt ist für den Betrieb eines Faserlasers eine hochwertige Sicherheitseinhausung notwendig, damit es zu keiner Gefährdung durch reflektierende Laserstrahlen kommt. Darüber hinaus gibt es regional unterschiedlich hohe Sicherheitsanforderungen, wie z. B. einen Lasersicherheitsbeauftragten. Diese Anforderungen führen zu vergleichsweise hohen Handlingskosten. Die Zugänglichkeit zur Wartung sowie zum Be- und Entladen des Schneidtisches ist eingeschränkt. Während bei Plasmaschneidanlagen eine flexible und einfache Be- und Entladung durch Stapler, Kräne oder auch manuell erfolgen kann, werden bei Laserschneidanlagen meist teure und komplexe Wechseltischsysteme eingesetzt.
Mit Plasmaschneidsystemen ist ein Mehrbrennerbetrieb auch an überlangen Brennschneidtischen möglich, was zu einer noch höheren Produktivität führen kann.
Schräg- und Fasenschnitte, insbesondere Mehrfachfasen, sind nach wie vor am besten mit Plasma umsetzbar: glatte gleichmäßige Fasen bis zu einem Winkel von 50° in einem Blechdickenbereich von 3 bis 60 mm. Eine qualitativ hochwertige und reproduzierbare Erzeugung von komplexen Mehrfachschnitt-Fasen (Y, K, X) ist mit heutigen Plasmaanlagen Stand der Technik. Der Laser hat beim Fasenschneiden physikalisch bedingt Nachteile.

Investment & Kosten
Ein realistischer und umfassender Vergleich der Kosten für beide Technologien ist schwer möglich, da in der Regel beide Verfahren für unterschiedliche Ansprüche (z. B. kleine Konturen) und Einsatzbedingungen eingesetzt werden.
Die Schneidkosten werden signifikant durch die Schneidgeschwindigkeit und die Auslastung beeinflusst, welche maßgeblich von der Blechdicke abhängen. Die Verschleißteilkosten sind bei Laserschneidanlagen zwar geringer, jedoch bieten Plasmaschneidsysteme Vorteile beim Gasverbrauch sowie bei den Wartungs- und Ersatzteilkosten.
Bezüglich der Investitionskosten sind moderne Plasmabrennschneidtische in der Regel deutlich günstiger als vergleichbare Laserschneidtische mit Wechseltischsystemen und Einhausung.
Zusammenfassung
Faktor | Faserlaser | Hochpräzisions-Plasma |
---|---|---|
Materialvielfalt | Baustahl, Edelstahl, Aluminium, Messing, Kupfer | |
Materialanforderungen | hoch | gering |
Blechdickenbereich | bis zu 60 mm | bis zu 160 mm |
Rechtwinkligkeit | ISO 1 | ISO 2 - 4 |
Bauteilgenauigkeit | unter 0,05 mm | 0,2 mm - 0,5 mm |
Rauheit | sehr hoch bis hoch | gering |
Minimale Schnittfugenbreite | 0,15 - 0,4 mm | 1 - 2,2 mm |
Schneidgeschwindigkeit < 10 mm | schneller | langsamer |
Schneidgeschwindigkeit > 15 mm | langsamer | schneller |
Investitionskosten | hoch | geringer |
Betriebskosten | gering | gering |
Sicherheitsanforderungen | hoch | gering |
Wartung | moderat bis hoch | moderat |
Das Team von Kjellberg Finsterwalde berät Sie gern ausführlich und erstellt eine entsprechende Kostenanalyse.
Fazit
Viele Kunden nutzen teure Lasersysteme, obwohl ihre Anwendung und Anforderung mit Plasma voll erfüllt werden könnten. Das Plasmaschneiden ist eine moderne und zukunftsfähige Technologie, die aus der metallverarbeitenden Industrie nicht wegzudenken ist. Aktuelle Plasmasysteme sind effizient, nachhaltig, leistungsfähig und flexibel.
Je nach Materialart, Blechdicke, Geometrie, Stückzahl, Schnittqualität und Werkstoff liegen die Vorteile hinsichtlich Wirtschaftlichkeit mal bei dem einen, mal bei dem anderen Verfahren. Die Anforderungen sollten im Vorfeld mit Hilfe von Wirtschaftlichkeitsberechnungen gründlich geprüft werden.