Gratings
HotWire – Plasma Cutting of Interrupted Structures
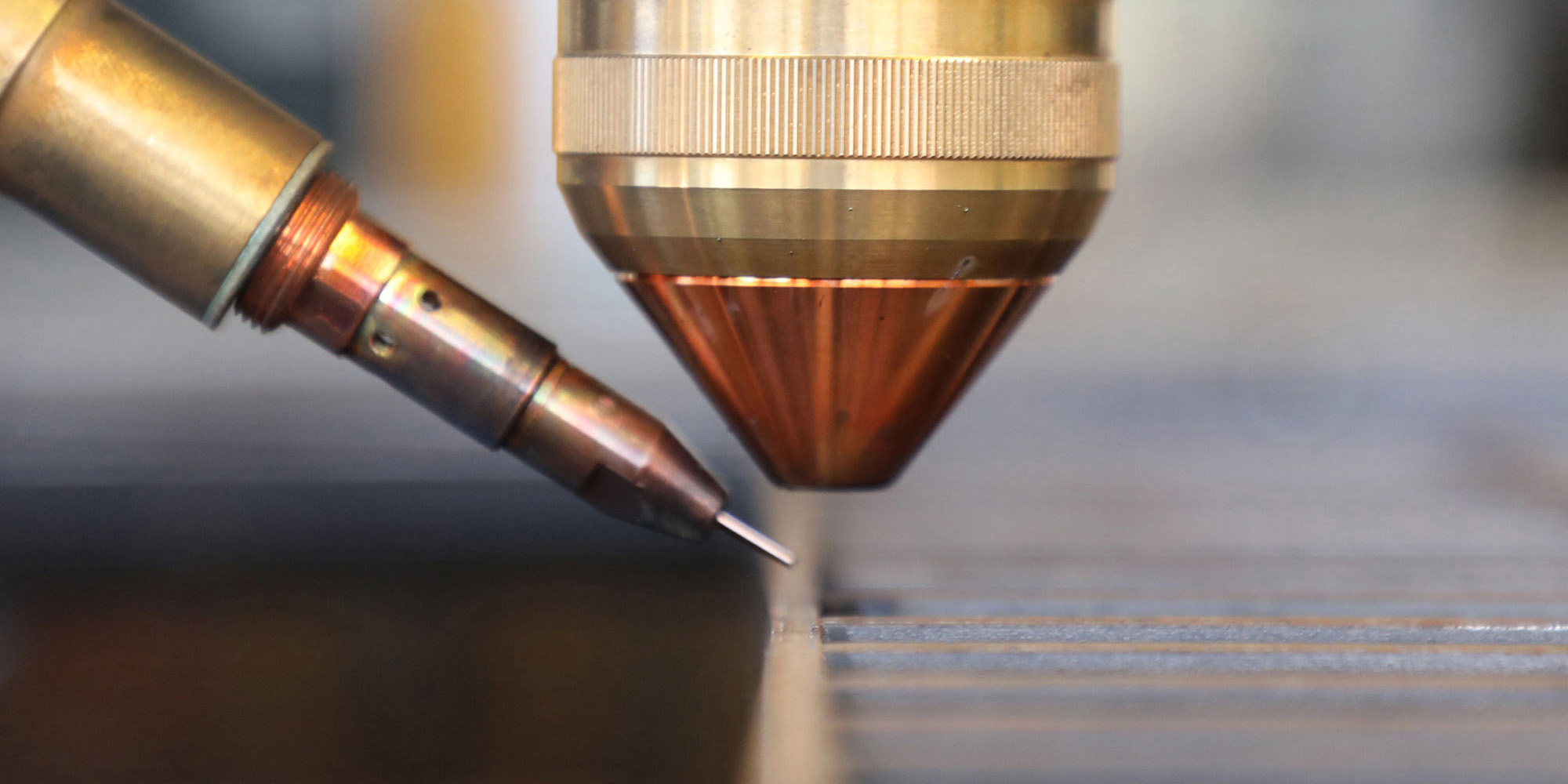
The patented HotWire method can be used to cut interrupted structures and non-conductive materials such as gratings and reinforced concrete, but also ceramics or glass.
The principle behind the method is indirect plasma cutting, with the plasma burning not between the cathode and the workpiece, but rather between the cathode and a wire which is continuously fed during the cutting process.
Advantages of the HotWire Method
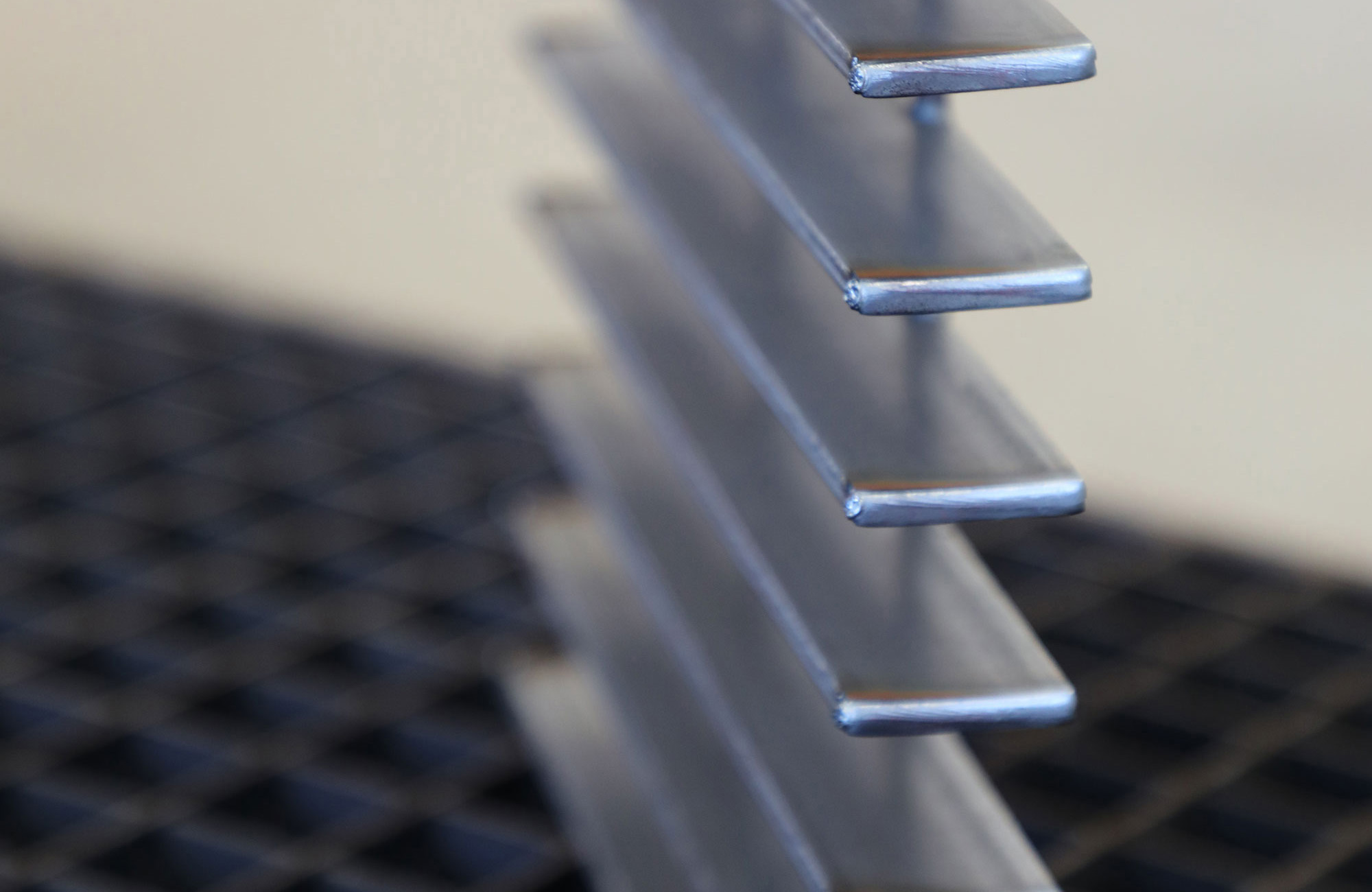
Unlike oxy-fuel cutting, the HotWire method can be used to cut different contours without additional preheating, without the use of a rotating head and regardless of direction. In contrast to the oxy-fuel process, gratings made of critical materials such as CrNi steel and aluminium can also be cut safely and reliably.
Depending on the plasma power source selected, cutting currents of 280 A or 360 A are available. Depending on the material, cutting current, size of the root face and required geometry, cutting speeds of up to 1.1 m/min are possible with good cutting quality. Because the arc is continuous, the load on the consumables is low, while process reliability is high.
In addition to the production of industrial grating, HotWire plasma cutting is also used in the dismantling of nuclear plants.
Suited power sources:
HiFocus 360i neo and HiFocus 440i neo
Further information: